Developer Interview: Fader Knobs Refined for Productivity and Motivation
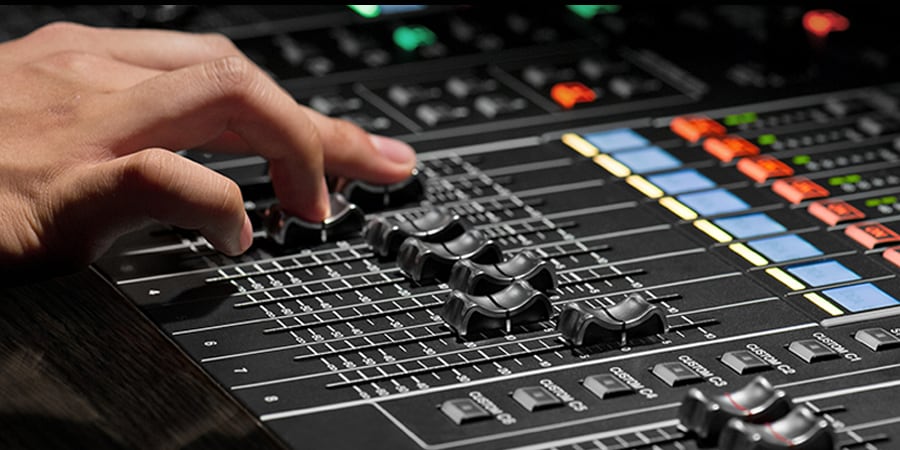
Amid the excitement and frenzy of a live music event there is a cool-headed mixing engineer making vitally important decisions and adjustments. Vocal, guitar, bass, keyboard, drum, and other faders must be precisely controlled to achieve the ideal musical balance. Yamaha’s mission is to support the engineer as he or she focuses intently on every moment of the ongoing musical program, fingertips poised on faders ready to make critical adjustments at any time. That mission led to a journey through a multitude of subtle refinements to the shape and dimensions of the mixing engineer’s most fundamental connection to the console: the fader knobs. The following interview reveals the depth of thought and care that went into the design of the evolved fader knobs introduced in the CL series digital mixing consoles.
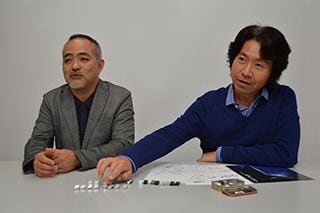
Left: Masaaki Okabayashi, CA mixer group manager at Yamaha’s PA development division. Joined Yamaha in 1987 and was involved in signal processing development from the early days of digital mixing. Mr. Okabayashi has worked on the DMR8, ProMix01, DM/0 series, PM5D, M7CL, LS9, CL/QL series, and is currently in charge of development.
Right: Masafumi Ito, chief designer of audio design group at Yamaha Design Laboratory. Joined Yamaha in 1991 and played a vital role in the design of electronic keyboards, digital drums, Clavinova, Electone, and a variety of other products. Mr. Ito is currently chief designer for PA products, having been involved in the CL series, RIVAGE PM10, and most other products in the current PA range.
What initiated the search for a new fader knob design?
Okabayashi:
It was Yamaha’s 25th anniversary of digital mixer production and we were on the brink of a new era, so we decided to apply some thought to one of the most important console features for mixing engineers who need to have intimate control over the sound at all times. Mr. Itoh and I began discussing the idea of going back to square one and working on a fresh fader knob design.
Ito:
Although there is an extensive variety of existing console designs, in terms of both function and appearance, we believed that there was room for improvement in the form, materials, and manufacturing techniques used for the console’s faders. We wanted to create parts that would be more functional as well as more appealing.
Masaaki Okabayashi, PA development division
How important are fader knobs to a mixing engineer?
Okabayashi:
For live music, the engineer’s influence in achieving the desired sound and musical expression is second only to the performers themselves. In terms of delivering the artistic expression that is taking place on stage to every member of the audience equally and with uncompromised quality, the mixing engineer bears the greatest responsibility. In a production situation the engineer is similarly responsible for delivering the best possible sonic quality to the end listener. Mixing is fundamentally a matter of balance. In the process of creating that perfect balance the mixing engineer spends most of his or her time operating faders, so the fader knobs become a key human interface.
Masafumi Ito, Yamaha Design Laboratory
Ito:
In a way they’re like the steering wheel of a racing car or the yoke of an aircraft. They have to be operated for long periods of time and allow delicate adjustments when necessary. They also have to be comfortable and familiar for consistent day-to-day use, while not producing stress in any way at any particular point. The big difference between a car or plane and a mixing console is that a single console has a multitude of faders that must be simultaneously operated with different fingers while providing immediate, accurate feedback of their relative positions. Fader knobs are a specialty tool that serves as the main point of contact between the operator and console, and they are the mixing engineer’s main means of expressing his or her sonic expertise and sensibilities. Although functionality is the most important criterion, the fact that the fader knobs will be used for entertainment also means that they should stimulate the operator’s imagination and motivation in the best possible way.
Describe the most important features of the new fader design.
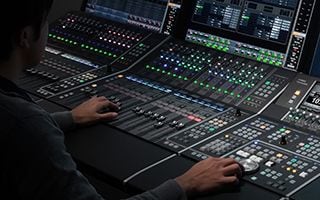
Okabayashi:
The three points we focused on were:
- Accurate expression of the engineer’s intent.
- Continuous operation for long periods of time without fatigue.
- Easy visual confirmation of the relationship between faders.
Ito:
Every detail of the design had to be meticulously tuned to achieve those three goals. While maintaining the basic dimensions of existing knobs, we worked to refine both functionality and appearance by increasing the width by about 1 millimeter, adding a left-to-right curve to the top to produce a more 3-dimensional shape, and providing a tactile insert at the center index. The result is a knob that is comfortable and precise to operate from any angle. Also, by making the front and rear surfaces somewhat concave it is easier to gradually raise the level by pushing the knob up from below, or to grip the knob between thumb and index finger and quickly move it to nominal, for example. At the same time the sides of the knob are recessed and open to provide a clearer view of the panel scale. The smoothly flowing metallic top plate and black base are visually integrated by the central non-slip insert, producing a unique look and feel that facilitates accurate operation from any position.
Describe the development process.
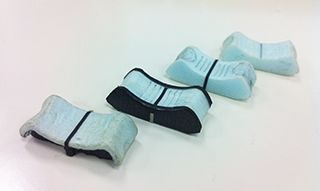
Okabayashi:
The process begins with the planner describing the concept to the industrial designer. In this case it was I who conveyed the concept Mr. Itoh. An industrial designer is normally not a mixing professional, so we began by having the designer visit a large number of mixing environments, talk to engineers, and acquire as deep an understanding as possible. That understanding could then be applied to the new design.
Ito:
We began by studying the strengths and weaknesses of existing designs, along with their precise dimensions, in order to decide which aspects should be kept and which needed to be refined. A number of ideas were then considered, using hand-drawn sketches and simple hand-made models. After the ideas were discussed with the development team and the general direction defined, more realistic models were produced for further consideration. Those models were presented to engineers at home and abroad, and the resultant feedback was applied to further refinements that, after adjustment for mass production, were incorporated in the final design.
How many countries were involved in the evaluation?
Okabayashi:
It was mainly North America, Europe, and Japan. The design was evaluated by a large number of engineers and system designers working in the live sound, production, and broadcast fields.
And how long did the entire process take?
Ito:
Fader knob design was undertaken as part of the overall console development project, spanning more than two years from start to finish.
Why was the new fader knob design implemented from the CL series onward?
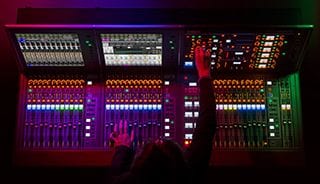
Okabayashi:
As Yamaha’s “next generation mixing consoles” the CL series had to offer significant improvements in both sound and operation. That same concept was carried on in the Nuage system, in the QL consoles, and in our flagship RIVAGE PM10.
Ito:
The new fader knobs were not designed exclusively for the CL series. They were designed to represent Yamaha’s vision for the future.
How has the marketplace responded to the new fader knobs?
Okabayashi:
The reaction has generally been that they have a unique, innovative form that offers an unprecedented balance of beauty and function.
Ito:
Our users are very pleased with both the functionality of the new knobs as well as the way their groundbreaking form enhances the overall appeal of our latest mixing consoles. And once again this is not about the knobs alone, but the CL series consoles, which were the first to feature the new fader knobs, have received a number of prestigious international design awards.
How do you expect the new fader knob design to affect the users’ experience?
Ito:
First and foremost we want engineers to be able to mix in their own personal style with minimum stress and fatigue. We also hope that the unique feel of the knobs contributes to increased motivation and morale, and that in turn results in more moving, meaningful music and events.
Okabayashi:
We want our users to enjoy the act of mixing as a tool to shape sound and music, and hope that these fader knobs play a role in elevating the artistry they convey to the audience.