Building a more sustainable Yamaha
We are continuing to manufacture musical instruments that are friendly to the environment and society so that we can share passion and performance with as many people as possible in the future.
This time, we will introduce our initiatives for wind instruments and percussion instruments.
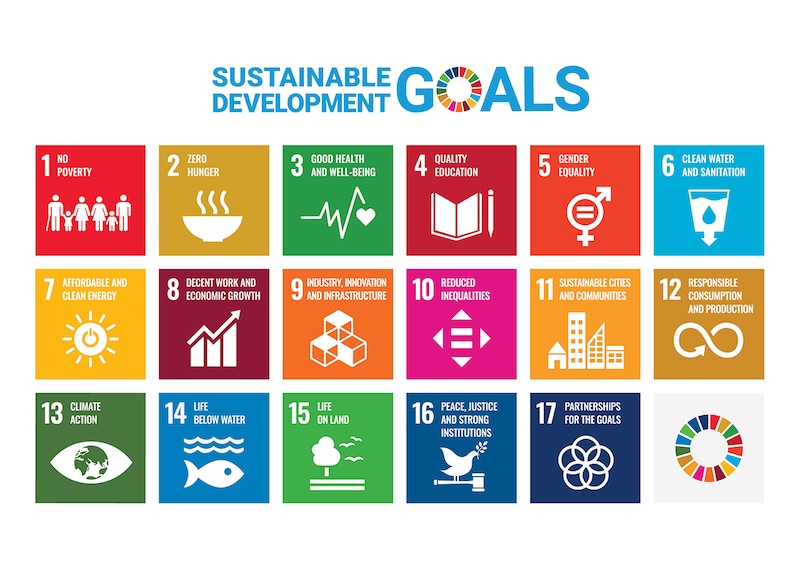
Corrugated cardboard for shipping: Transitioning to a print design and method that reduces impact on the environment
Packaging with Purpose: Reducing Our Environmental Footprint
At Yamaha, our commitment to quality extends beyond sound, starting with the way our instruments are packaged. We’ve redesigned the packaging for our wind instruments to align with our broader sustainability goals—minimizing environmental impact while preserving protection and presentation.
Greener Packaging from the Start
Each Yamaha wind instrument is carefully packed in corrugated cardboard to ensure safe delivery. Although this packaging plays a crucial role in transit, it’s typically discarded after unboxing. To reduce its environmental impact, we’ve adopted more sustainable materials and production methods that enhance both efficiency and responsibility.
Eco-Friendly Printing with Water-Based Inks
We’ve transitioned from conventional oil-based offset printing to flexographic printing using water-based inks. This shift significantly reduces the generation of volatile organic compounds (VOCs) and wastewater, creating a cleaner, safer process for both people and the planet.
Reduced Energy Use Through Smarter Printing
The new printing method not only lowers emissions—it’s also more energy efficient. By streamlining the process, we’ve cut printing time by approximately two-thirds compared to conventional techniques, resulting in a substantial reduction in electricity consumption during production.
Smarter Design, Bigger Impact
・ 100% Recycled Paper: By designing around the natural tones of recycled paper, we increased recycled content from 85% to 100%.
・ 90% Less Printed Area: We reduced the printed area significantly, lowering ink usage while keeping branding clear and effective. These improvements are currently implemented across select entry-level wind instrument models. Packaging designs may vary by region and product.
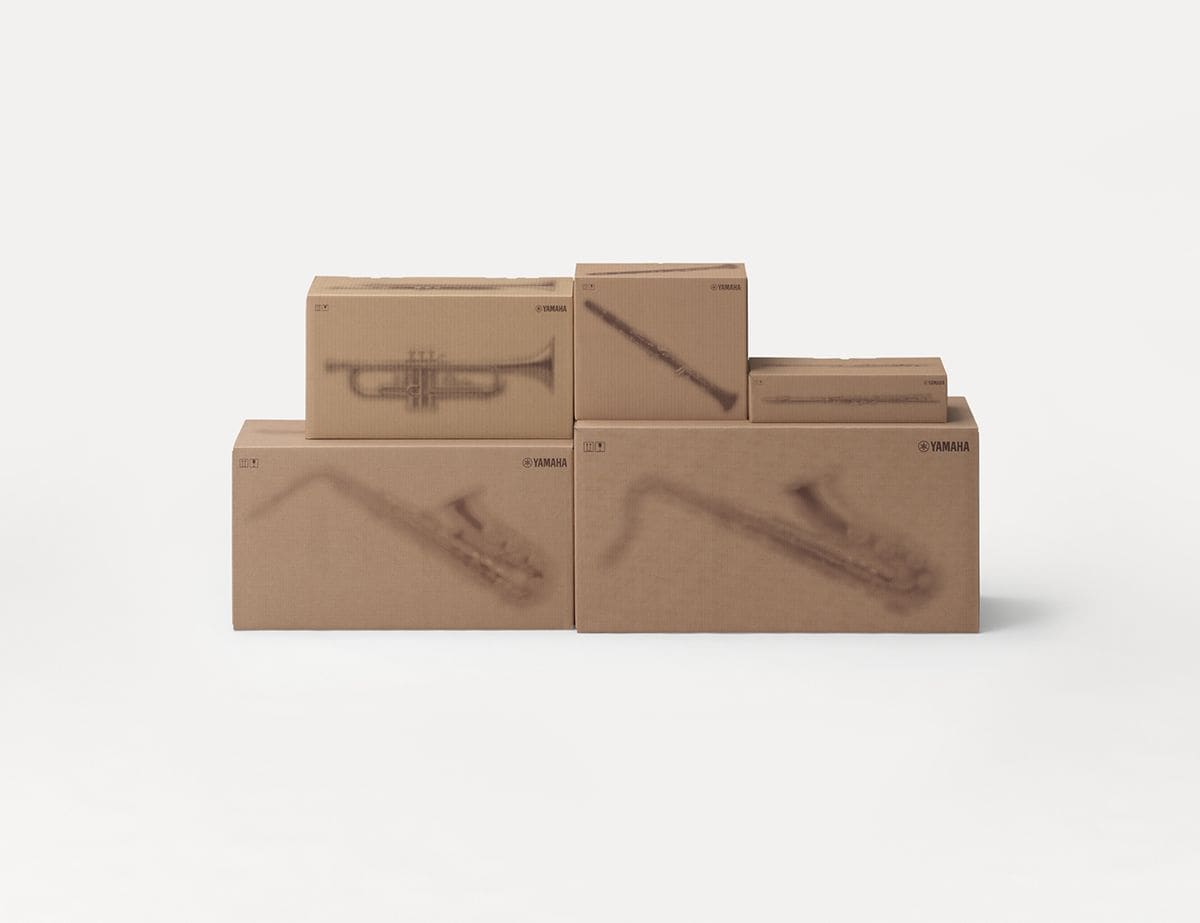
Afforestation in Tanzania in cooperation with local communities
The bodies of clarinets, oboes and piccolos are made from the black, solid lumber Grenadilla (African Blackwood). The country of origin is the United Republic of Tanzania in Africa.
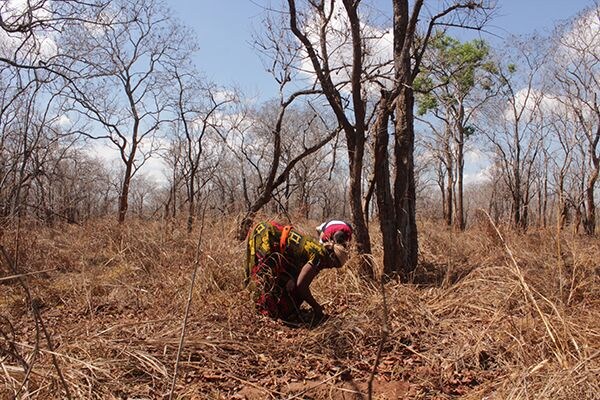
Grenadilla is indispensable for manufacturing of musical instruments, but it is said that it has a possibility to become extinct in the future.
Therefore, Yamaha is promoting afforestation activities together with Tanzanian NGOs and residents. So far, we have been able to plant about 7,400 trees in four years.
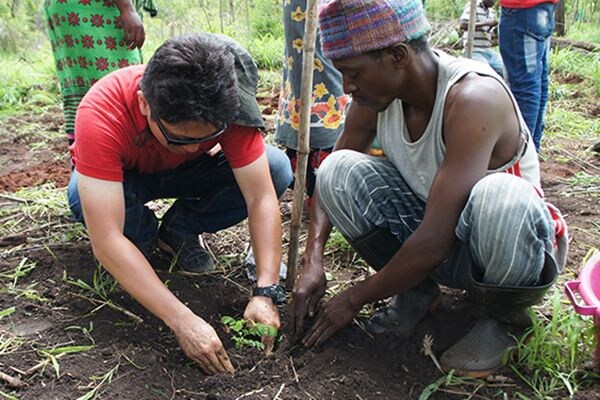
It takes more than 100 years for trees to grow to the size that can be used for musical instruments. To ensure that forests and musical instruments will continue 100 years from now, Yamaha is addressing toward the future while working with its partners, the villagers.
In this initiative, 95% of turnover from logging and sales are village revenues. Thanks to this structure, new elementary school and village offices have been established, and new beds and mattresses have been brought to clinics. In addition, we are enriching the lives of women by providing them with hospital expenses and allowances for children to go on to school.
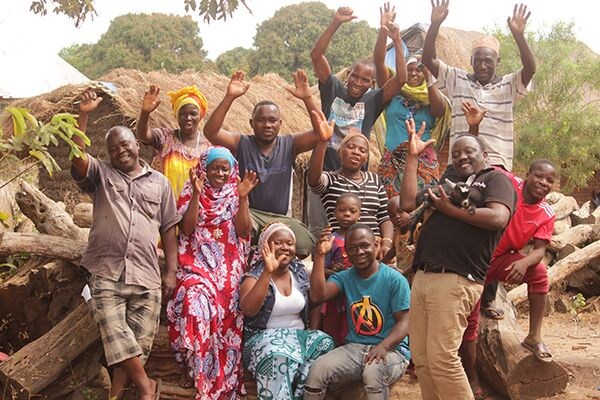
Other promises that we have made
- Procure timber taking priority to timbers from certified forests
- Use legally cut and traded lumber with clear supply sources
- Confirm that there is no human rights violation in the place of origin or other bad effect
- Not to use genetically modified tree species
- Use existing resources as efficiently and carefully as possible. Continue basic research for this purpose
Maintenance products for wind instruments: Transition to paper packaging
As we reconsider the use of disposable plastics from the perspective of environmental impact, Yamaha is working to reduce the use of these in packaging materials. As part of this effort, Yamaha is transitioning to paper packages for some of our maintenance products for wind instruments. As the packages are made of 100% paper materials, they can be recycled as paper.
Environmentally friendly recorder made of bioplastic
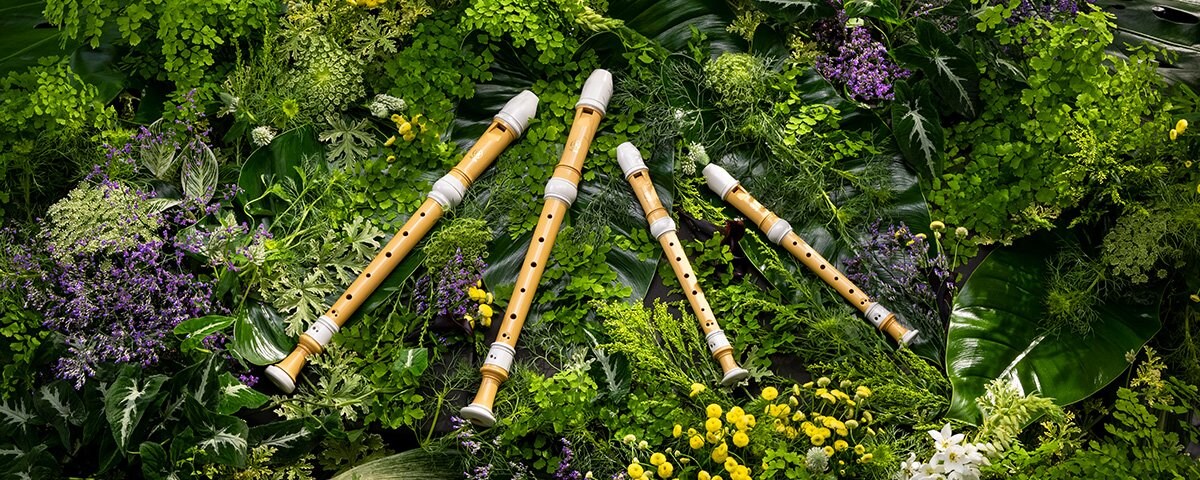
The Yamaha recorder made of bioplastic, which uses the environmentally friendly and musically superior biomass material Unitika "Terramac®" for its body, is the world’s first application of environmentally friendly plant-based materials in a musical instrument. Note: As a musical instrument commercially available, according to our own research in June 2014.
Terramac® biomass material
Terramac® is an environmentally friendly material made from plant-based polylactic acid (PLA), which is combined with other materials, modified, and molded using Unitika's proprietary technologies. It is currently widely used in products ranging from food containers to electronic device parts. By using this "Terramac®" material for recorders, Yamaha has reduced CO2 emissions while maintaining the same durability, strength, and appearance as conventional acrylonitrile butadiene styrene (ABS). This will contribute to the development of a more sustainable society through the manufacturing of high-quality instruments while at the same time mitigating the impact of climate change and reducing the use of chemicals.
Polylactic acid (PLA): A type of biomass-based plastic made from lactic acid, which is produced by fermenting plant-based sugar. The amount of CO2 emitted during combustion of PLA is much lower than that of other plastics. Furthermore, since the raw materials, plants, absorb CO2 from the atmosphere as they grow, the amount of CO2 emissions, which is considered a cause of climate change, can be significantly reduced. The combustion heat, at one-half to one-third that of petroleum-based plastics, is also low and of course, no toxic gases such as dioxin or hydrogen chloride are emitted when it is incinerated.
Why are plant-based plastics environmentally friendly?
1. Reduced CO2 emissions: Plants grow by absorbing CO2, which is a cause of global warming. While plant-based plastics produce the same amount of CO2 emissions as other materials during manufacture, use, and disposal, the total amount of CO2 generated is reduced by the amount absorbed during plant growth.
2. Reduced petroleum use: Petroleum is the main raw material for plastics, but oil reserves are limited and will be exhausted at some point in the near future. By replacing part of the raw material requirements with plant-based materials, the total amount of petroleum used can be reduced, thereby extending the life of available fossil fuel resources.
World’s First Mass Production of Musical Instruments
Using Lead-free Solder
In the wind instrument factories, many processes are performed manually by craftsmen, one of which is soldering-bringing together fine metal parts.
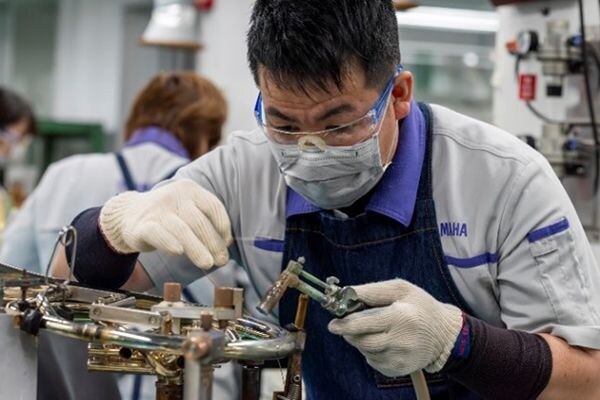
Generally, lead is used for soldering. However, lead may have a negative impact on human health or contaminate the environment in which animal and fish are living.
In order to manufacture musical instruments that are friendly to humans and the environment, Yamaha has conducted a number of studies and succeeded in mass-producing wind instruments using lead-free solder for the first time in the world.
Currently, all the wind instruments* shipped from Yamaha factories use lead-free solder.
*Excluding gold flutes
Reduction of formaldehydrocarbons
Not only wind instruments but also percussion instruments are being implemented.
Formaldehyde, which is contained in adhesives for wood, is known as one of the causative substances of sick house syndrome.
To reduce formaldehyde to the limit, Yamaha has improved equipment, adhesives, and processing conditions at its percussion factory. All of Yamaha's percussion instruments, which have been shipped since 2009, have met the standards of the Ministry of Health, Labour and Welfare.
Efforts to Protect Environment at Yamaha Wind Instrument Factories
Yamaha manufactures wind instruments at factories in Shizuoka Prefecture, Japan, China and Indonesia.
When making wind instruments at a factory, a large amount of water is required to cooling the heated and processed parts, cover the metal membrane on the surface (plating), and cleaning the musical instrument. In addition, a large amount of waste liquid is generated.
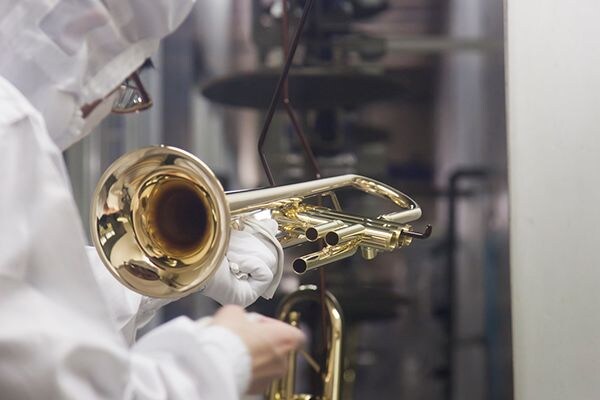
To conserve water, Yamaha has been working since 1970 on the use of recycled water and measures to prevent leakage of harmful substance. For example, we are continuing to conduct periodic surveys to check whether plant wastewater has had an impact on water quality and living things so as not to have a negative impact on rivers or the sea. Currently, we have confirmed that there is little impact on ecosystem.
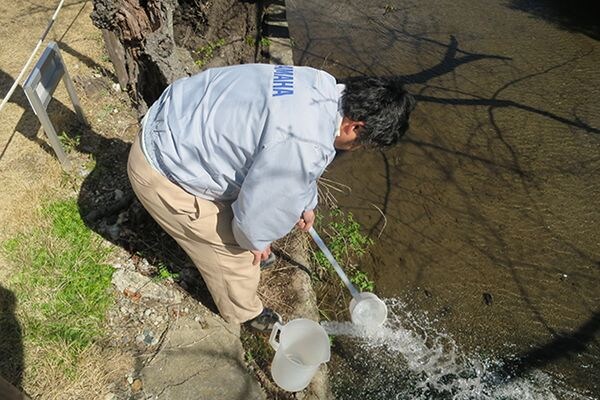
Initiatives at Each Factory
Toyooka Factory, Japan
The equipment was newly introduced in 2010. We have concentrated acidic and alkaline emissions from manufacturing processes and reduced their emissions by approximately 80%.
Xiaoshan Factory, China
Currently, about 80% of wastewater is reused, clearing the Zhejiang Province law. Under this law, standards are set more stringent than general plant wastewater standards.
Cooling water which is required when components made of copper in wind instruments are heated and processed is circulated and reused. This initiative reduces water consumption by approximately 5700 tons per year.
Yamaha Musical Products Indonesia
Currently, more than 60% of plant wastewater is reused. We are also working to reduce the amount of chemicals used.
Not only wind instruments but also recorders' production processes recycle and use cleaning water. This reduces water consumption by approximately 12,000 tons per year.